How to improve productivity in your construction company
Posted 4 years ago
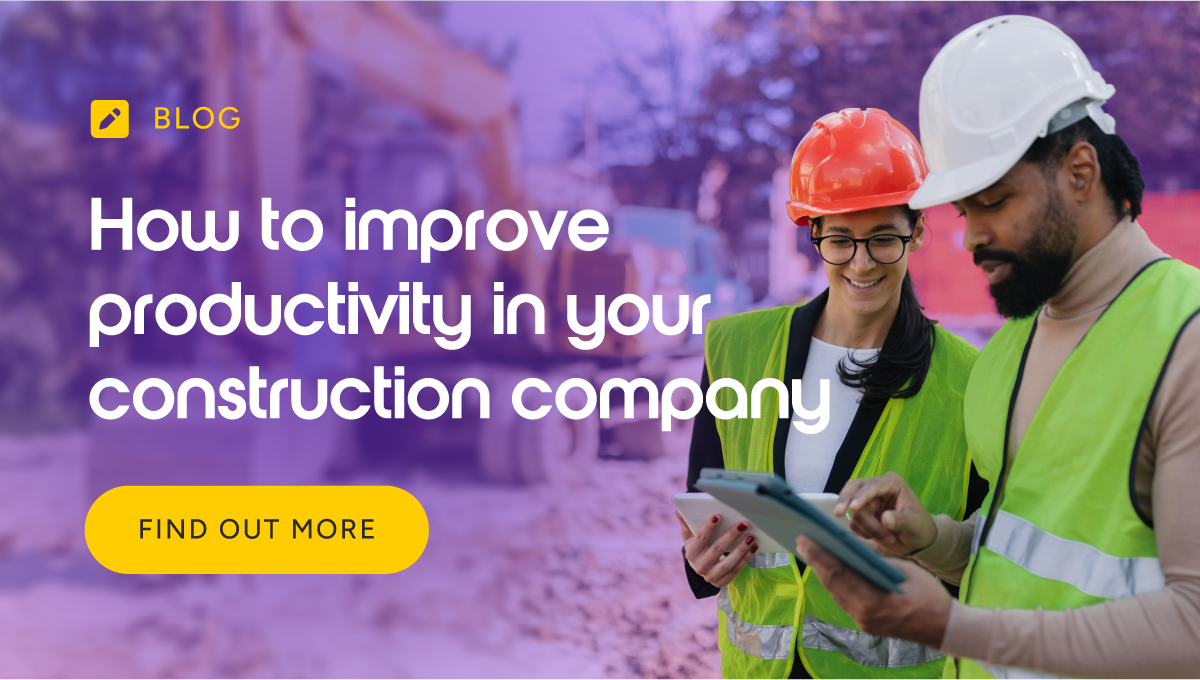
As with many industries, construction has been one of those hit by a massive skills shortage off the back of the pandemic and economic struggles. But the sector has, for some time, been known for its inefficiencies when it comes to productivity. We look at some of the reasons for this, as well as what can be done to help improve productivity within construction companies.
What is productivity in the construction industry?
Productivity in the construction industry refers to how efficiently resources such as labour, materials, and equipment are used to complete projects on time and within budget. It is typically measured by output per worker or per hour worked, but it also extends to overall project efficiency, minimising delays, and optimising resource allocation.
Unlike office based industries where work is often predictable, construction productivity is influenced by several external factors. The complexity of projects, changing site conditions, weather disruptions, and reliance on subcontractors all make construction inherently more challenging to standardise. A single delay, whether due to material shortages, unexpected site conditions, or miscommunication, can have a domino effect on the entire project timeline.
Low productivity doesn’t just mean slower work; it directly affects profitability. The UK construction sector already faces a significant productivity challenge, with studies showing that construction productivity growth has lagged behind other industries for decades. Inefficiencies lead to increased labour costs, wasted materials, and missed deadlines, all of which chip away at profit margins. On the other hand, improving productivity can enhance project success, ensuring deadlines are met, costs are controlled, and clients remain satisfied, ultimately helping businesses stay competitive in a demanding market.
Why is productivity important in construction?
Productivity is a key factor in the success of any construction project. High productivity means that workers, materials, and equipment are used efficiently, leading to faster completion times, lower costs, and improved safety. In an industry where delays and budget overruns are common, optimising productivity can make a significant difference to your bottom line.
- Reduced costs and waste
When productivity is high, resources are used efficiently which minimises unnecessary costs. Labour, equipment, and materials are some of the biggest expenses in construction, so reducing waste and avoiding rework can lead to significant savings. Studies have shown that the waste the construction sector produces contributes a 1/3 of the UK’s total yearly waste amount. This can be due to poor planning, miscommunication, or project delays. By streamlining processes and improving coordination, companies can maximise their budgets and stay competitive.
- Faster project completion
Delays in construction can be costly, leading to penalties, increased labour expenses, and dissatisfied clients. High productivity ensures that tasks are completed on schedule, keeping projects on track. A McKinsey study found that large construction projects typically take 20% longer to finish than planned, highlighting the widespread issue of inefficiency. By focusing on improved scheduling, better communication, and upskilling workers, companies can speed up project completion without compromising quality.
- Improved worker satisfaction and retention
An organised and productive workplace leads to higher job satisfaction. Workers who have clear expectations, proper training, and access to the right tools are more engaged and motivated. Conversely, inefficient processes, frequent rework, and poor site management can frustrate employees, leading to high turnover rates. Given the ongoing skills shortage in construction, retaining experienced workers is crucial. Investing in training and improving workflows not only boosts productivity but also creates a more stable workforce.
- Enhanced safety and reduced incidents
Safety and productivity go hand in hand. A disorganised site with rushed workers and unclear communication is far more likely to result in accidents. According to the Health and Safety Executive (HSE), around 60,000 construction workers suffer non-fatal injuries each year in the UK, with many incidents linked to poor planning or fatigue. High productivity means having detailed schedules, adequate rest periods, and clear safety policies, all of which help prevent accidents and keep workers safe.
For construction businesses, improving productivity is not just about working faster, it’s about working smarter. When teams are properly trained, processes are optimised, and projects run efficiently, companies see lower costs, faster turnaround times, happier employees, and safer job sites.
What are the effects of low productivity in construction?
Low productivity in construction has plenty of negative consequences, including affecting project timelines, costs, worker safety, and overall business reputation. Given the industry’s tight margins and high competition, inefficiencies can quickly lead to significant financial and operational setbacks.
- Project delays and increased costs
When productivity is low, tasks take longer to complete, causing project timelines to slip. Delays often result in increased labour costs, extended equipment rentals, and penalties for missing deadlines. These overruns not only impact profitability but also create a ripple effect, delaying future projects and straining client relationships.
- Higher accident rates
Poor productivity is often linked to rushed work, miscommunication, and worker fatigue—all of which contribute to safety incidents. A study by the Health and Safety Executive (HSE) found that time pressure and lack of proper training are common factors in construction accidents. When workers are overworked due to inefficient processes, they are more likely to cut corners, leading to a higher risk of injuries. Construction already accounts for around 30% of all workplace fatalities in the UK, making it essential for companies to prioritise both efficiency and safety.
- Lower profit margins
Low productivity directly translates to increased costs per unit of output, squeezing already tight profit margins in the construction sector. When projects take longer than necessary due to inefficient processes, companies incur higher labour expenses, longer equipment rental periods, and increased overhead costs. The UK construction industry, known for its competitive bidding and often slim margins, is particularly vulnerable to the impact of wasted resources and time. For example, if a task takes twice as long as it should, the labour cost associated with that task effectively doubles, directly reducing the project’s profitability. In a market where clients are often highly price-sensitive, companies struggling with productivity find it difficult to absorb these extra costs and remain competitive, ultimately leading to diminished profits on each project.
- Unhappy Clients and Damaged Reputation
Construction projects rely on strong client relationships, and delays, budget overruns, and quality issues can severely impact customer satisfaction. A client who experiences poor service is unlikely to return or recommend the company, potentially leading to lost business opportunities. In an industry where word-of-mouth and reputation play a huge role, consistently delivering projects on time and within budget is crucial for long term success.
Low productivity isn’t just an internal issue, it affects every aspect of a construction business, from financial stability to worker safety and client satisfaction. By addressing inefficiencies, investing in training, and improving planning processes, companies can avoid these issues before they happen, and build a stronger, more competitive business.
What causes low productivity on construction sites?
Productivity in construction is influenced by many factors, and even small inefficiencies can lead to costly delays and budget overruns. Understanding the root causes of low productivity can help businesses take proactive steps to improve efficiency.
-
Poor planning and scheduling
A comprehensive project plan is essential for keeping work on track, yet many construction projects suffer from mismanaged timelines, incomplete scheduling, and unrealistic deadlines.
Poor planning can lead to:
- Gaps in workflow where teams are left waiting for materials or instructions.
- Overlapping tasks that cause bottlenecks.
- Late-stage project changes that require costly rework.
To avoid these issues, businesses should use construction project management software and ensure that detailed schedules are created and regularly updated.
-
Lack of skilled labour
The construction industry has been facing a skills shortage for years, and without experienced workers, projects take longer and errors become more frequent. According to the Construction Skills Network (CSN) report, the UK needs over 250,000 new construction workers by 2028 to meet demand. The lack of skilled labour leads to:
- Lower work quality, resulting in rework and wasted materials.
- Increased pressure on existing staff, leading to burnout.
- Delays in project completion due to a slower pace of work.
Investing in training and upskilling existing workers can help bridge the skills gap and improve overall efficiency.
Ineffective communication
Miscommunication is a major cause of delays and mistakes in construction. When project managers, site supervisors, and workers are not aligned on schedules, materials, or safety procedures, it can lead to:
- Workers are waiting for instructions or working on incorrect tasks.
- Misinterpretation of blueprints or specifications, requiring costly corrections.
- Safety hazards due to unclear site protocols.
Using digital communication tools, such as mobile apps that provide real-time updates, can help teams stay informed and reduce misunderstandings.
Outdated technology and equipment
Many construction companies still rely on outdated methods, which slow down progress. The adoption of new technology, such as drones, automation, and AI-driven project management tools, has been slow in the sector. Relying on outdated equipment or techniques can result in:
- Increased manual labour and inefficiency.
- Frequent equipment breakdowns, causing unplanned downtime.
- Inconsistent quality and higher error rates.
Upgrading to modern equipment and adopting digital tools can help improve efficiency, reduce errors, and streamline operations.
Worker fatigue & motivation
Construction is a physically demanding job, and long hours without proper rest can lead to exhaustion, reduced concentration, and increased mistakes. Productivity drops when workers are:
- Overworked and struggling with fatigue.
- Demotivated due to a lack of incentives or career progression.
- Experiencing a stressful or unsafe work environment.
To combat this, businesses should implement better shift management, offer performance incentives, and create a positive work culture to keep employees engaged. Want to learn more about improving motivation with your workers? Take a look at our blog So, why is mental ill-health such a problem in the construction sector?
Weather and external factors
Unlike office based industries, construction is highly dependent on external conditions. Bad weather such as heavy rain, snow, or extreme heat can halt outdoor work which causes delays.
Other external factors include:
- Supply chain disruptions are affecting material availability.
- Regulatory changes that impact project compliance.
- Site specific challenges, such as unexpected ground conditions.
While weather is uncontrollable, companies can mitigate its impact by planning for seasonal disruptions, using prefabricated materials to reduce on-site work, and improving supply chain resilience.
Low productivity in construction is often the result of multiple factors working together. By addressing planning inefficiencies, investing in skilled labour and technology, improving communication, and prioritising worker wellbeing, businesses can create a more productive and profitable work environment.
How can you increase productivity in the workplace?
Construction companies can start to make improvements in their productivity rates by considering the following:
Embrace technological advancements: A lack of investment in technology can slow down construction projects and mean productivity is lower than what it could be. Using software and mobile apps allows for progress to be tracked more easily, smoother processes and real-time data collection. For example, Project Management Software can help with storing data, stock management, scheduling, budgeting and team collaboration. Keeping track of all these details in one central location not only saves time but keeps accurate records of information.
Improve communication and planning: A lack of communication is a common cause of inefficiency in a construction company. Ineffective communication between the office and job site can cause delays and errors. Ensuring your workers understand the importance of communicating and meeting deadlines will help instill a culture where productivity is at the forefront of everyone’s minds. This is where technology can have a huge benefit, as mobile apps can instantly update workers with key information.
Collecting data from projects will also help companies gain insights when it comes to productivity. This will allow for improved processes and more accurate budgeting and timescales. Allowing the team to understand the workflow before a project starts will help keep them on track, and the use of data will mean project forecasts are more accurate to achieve greater job efficiencies.
Focus on safety & training: According to the HSE, the construction industry incurred the greatest number of fatal injuries in 2023/24. Therefore it’s vital that construction sites put safety first and ensure employees receive the correct training for their role to minimise the risk of injuries and fatalities. Having a well trained workforce will help your employees feel more confident when it comes to working onsite and will have a positive effect on their productivity.
eLearning courses can be particularly useful for a range of topics from working at height to asbestos awareness training. eLearning is cost effective, and allows workers to fit training in at a convenient time. On the job training can also be valuable to help workers gain a deeper understanding of a particular specialism.
Improve your workplace culture: A company’s culture cannot be changed overnight, but working to improve it can ensure your employees are more motivated and productive. Gradually communicating messages about the importance of taking regular breaks, minimising overtime and working to increase productivity will help employees feel more satisfied and valued in their roles. Investing in training to keep them safe or knowledgable about new innovative technology will help keep them engaged and their performance at its highest.
Recruit more skilled workers: It is known that there is a lack of skilled workers in the construction industry but attracting talent to your organisation is key to having the best team and chance of business success. Digital advancements are also causing a skills gap and therefore recruiting experienced managers to lead your team and support with any new technologies will be vital to help improve efficiency and productivity. If you are looking for some tips on recruitment and retention in construction download our free guide, created in partnership with Citation.
There are other factors which can help improve productivity in construction but starting to take some steps to improve productivity will pay off, whether this is through increased employee morale, quicker completion of projects, better profit margins or even winning more bids.
How To Measure Productivity on A Construction Site
Measuring productivity in construction is essential for identifying inefficiencies and improving project outcomes. Unlike traditional office settings, where productivity can be tracked through output or revenue, construction sites require a combination of key performance indicators (KPIs) to assess efficiency. Below are the most important metrics used to measure productivity in construction.
Labour Productivity
Labour productivity is one of the most critical metrics for assessing efficiency on a construction site. It is typically measured as:
- Output per worker per hour – The amount of work completed relative to the time spent.
- Workforce efficiency – The percentage of time workers spend on productive tasks versus idle time.
A decline in labour productivity may indicate issues such as poor planning, lack of training, or inefficient worksite organisation.
Project Completion Rates vs. Deadlines
Tracking how well a project progresses compared to its original timeline helps identify potential delays early. Key measurements include:
- Planned vs. actual progress – Comparing scheduled milestones with actual completion rates.
- Percentage of tasks completed on time – Helps determine whether deadlines are being met or consistently missed.
Regular progress tracking can help businesses adjust schedules, allocate resources more effectively, and avoid costly overruns.
Downtime Analysis
Downtime, when workers or equipment are idle due to preventable issues, can significantly reduce productivity. Common causes of downtime include:
- Waiting for materials or equipment.
- Poor weather conditions.
- Unclear instructions or delays in approvals.
By identifying patterns in downtime, project managers can improve scheduling, streamline logistics, and reduce unnecessary delays.
Rework Percentages Due to Errors
Rework is a major productivity drain, leading to wasted materials, increased labour costs, and project delays. Some common causes of rework include:
- Poor communication and misinterpretation of plans.
- Low-quality workmanship due to lack of training.
- Incorrect or defective materials being used.
Tracking rework percentages allows companies to pinpoint problem areas and invest in better training, clearer communication, and quality control measures.
Tools & Software for Productivity Tracking
To improve accuracy and efficiency in measuring productivity, many construction firms are using digital tools, such as:
- Construction project management software – Tools like Procore, Autodesk Build, and Buildertrend help track project timelines, team performance, and material usage.
- Time-tracking apps – Apps such as Raken and ClockShark monitor work hours and identify inefficiencies.
- Drones & AI-powered analytics – Drones can provide real-time site data, while AI-driven insights help predict delays and suggest process improvements.
Measuring productivity on a construction site is key to reducing costs, improving efficiency, and ensuring projects stay on schedule. By tracking labour efficiency, project timelines, downtime, and rework rates, businesses can gain valuable insights and make informed decisions to boost productivity.
Online Construction Training Courses to Increase Worker Productivity
Struggling with delays, wasted materials, and the ever growing skills gap? You’re not alone. The UK construction sector faces serious productivity hurdles. But there’s a solution: empower your team with our focused online training. From mastering project management to minimising material waste, our courses deliver practical skills that drive real results. Stop letting inefficiencies eat into your profits. Discover how our construction eLearning can transform your projects. Request a quote today or try out our courses for free!
Related articles
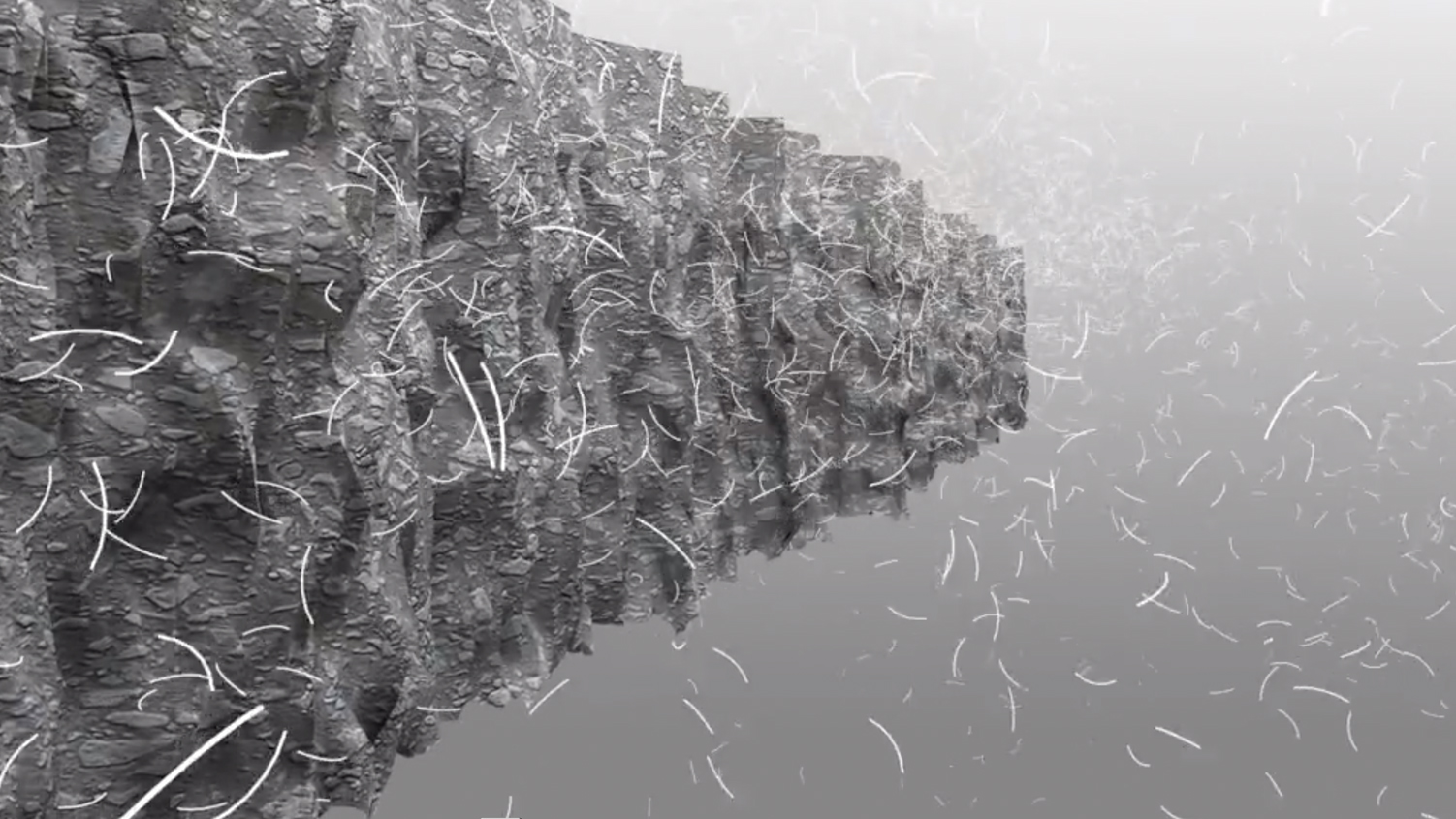
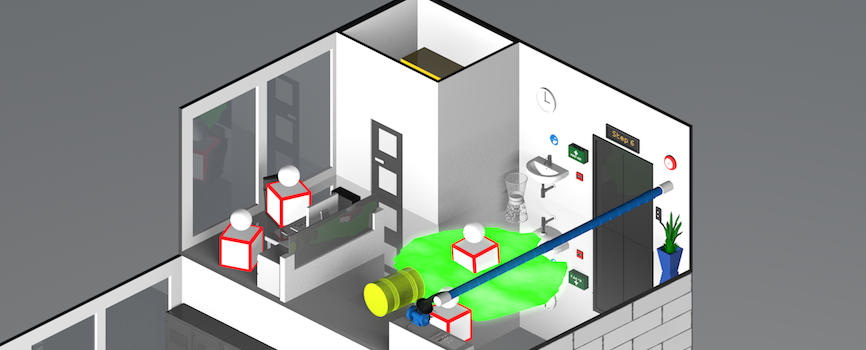
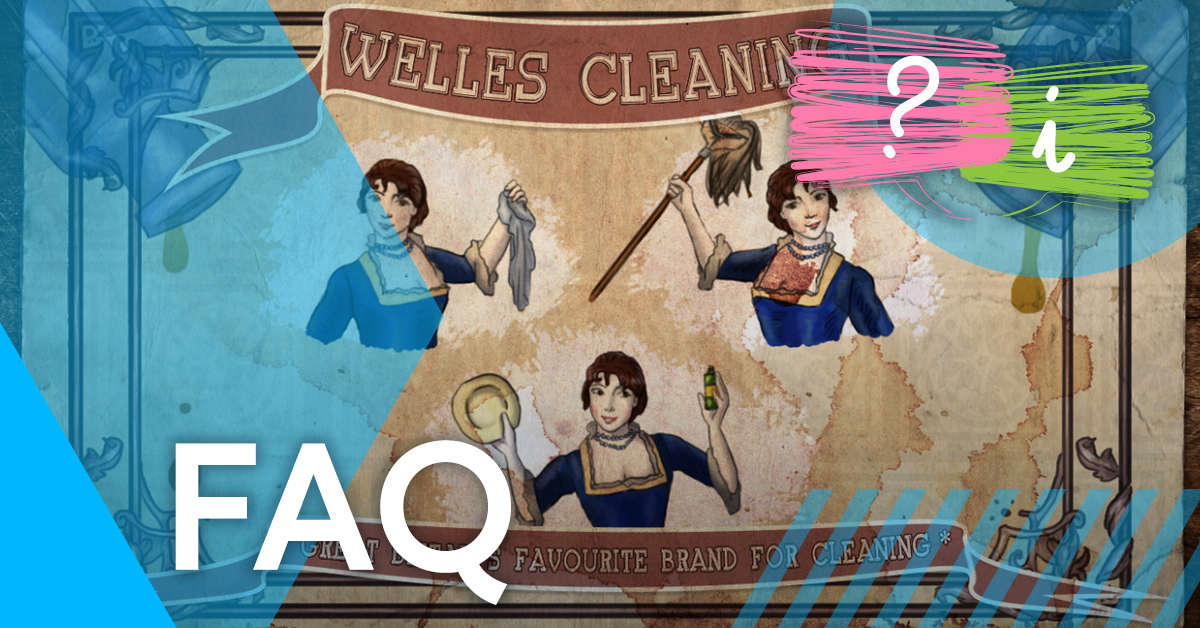
Opt-in to our newsletter
Receive industry news & offers