What is LOLER?
Posted 6 years ago

Lifting operations can be incredibly dangerous – whether it’s a forklift raising heavy pallets in a warehouse, a rope and pulley system hoisting a window cleaner up the side of a skyscraper, or a crane positioning steel beams in a construction site – it’s crucial that nothing goes wrong.
LOLER (Lifting Operations and Lifting Equipment Regulations) are a set of regulations designed to make lifting operations, and the use of lifting equipment, as safe as can be. The regulations make sure that you select strong and stable equipment; position it in a suitably safe location; impose a system of regular checks, thorough inspections, and routine maintenance; and store equipment in a safe location, helping to prolong its usable life.
It also requires you to carefully plan every use of your equipment, taking into account all foreseeable risks; whilst also keeping any relevant safety records (EC Declarations of
Conformity, thorough inspection reports, details of safe working loads, etc.). It places a duty on anyone managing a lifting operation, or the general use of lifting equipment, to make sure that operators are properly trained, and have enough experience to complete the job safely.
What equipment is covered by LOLER?
LOLER, very specifically, only applies to the use of lifting equipment for work purposes. This means, for example, that customer lifts in a shopping centre are not covered, since they’re not used for work purposes; whereas a goods lift used by staff, is. Escalators have their own set of regulations, so aren’t covered by LOLER, and pallet trucks and dentist chairs are considered low risk enough not to be covered either.
However, it’s important to note, that whilst a particular piece of equipment may not be covered by LOLER, it is still most likely covered by the Provision and Use of Work Equipment Regulations (PUWER) – which enforces similar responsibilities for selection, inspection, maintenance, and training. Also, the Health and Safety at Work Act places a responsibility on employers and the self-employed for the safety of anybody potentially affected by their work – this includes employees, customers and passers-by. So, while you may escape from LOLER, you’ll almost certainly be covered by another piece of legislation.
The effects of not complying with LOLER
The effects of not complying with LOLER can be catastrophic. In 2016, a London based crane hire company was fined £750,000 plus further legal costs after one of their cranes collapsed. This resulted in the deaths of both the crane operator and a member of the public who happened to be nearby. A subsequent investigation found that the company had an inadequate system for inspecting and maintaining their equipment, which led to a row of ring bolts being weakened through wear and tear. Under the strain of a heavy load, these bolts broke off, causing the crane to topple. Had the company fulfilled its LOLER obligations, it would have saved hundreds of thousands of pounds; a loss of time, work, and reputation; and most importantly, it would have saved two lives lost due to negligence.
LOLER Legislation
As previously noted, LOLER was put in place to ensure that lifting operations are carried out as safely as possible. They should be planned, supervised, and conducted in a safe manner, by competent and well-trained people. As well as ensuring all equipment is fit for purpose, appropriate for the task, and that all records are up-to-date.
The HSE advises that where you undertake lifting operations, you must:
- plan them properly
- use people who are sufficiently competent
- supervise them appropriately
- ensure that they are carried out in a safe manner
What is a lifting operation?
LOLER defines a lifting operation as ‘… an operation concerned with the lifting or lowering of a load’. A ‘load’ is the item or items being lifted, which includes a person or people.
What is lifting equipment?
Lifting equipment means the equipment used at work for lowering and lifting loads. This will include accessories and attachments that support, anchor, or fix to the equipment.
Responsibilities LOLER puts on employees and employers
That all equipment should be suitable for purpose, any hazards must be assessed and reduced or, if possible, eliminated altogether.
Equipment should meet certain standards to perform the tasks required e.g. BS, ISO, EN, CEN/CENELEC. These are used as a rule, guideline, or definition to be recognised.
Anyone using the equipment should be suitably trained and all equipment should come with a set of instructions on how to use them. Employers should then make sure employees are aware and understand these instructions and that they use equipment correctly.
Equipment should be well maintained in a safe condition. It is good practise to conduct pre-use inspections before equipment use. It also outlines requirements for the formal inspection of lifting equipment at regular intervals.
Other Legislation
Personal Protective Equipment at Work Regulations 1992
This legislation works towards reducing the risk of accidents by using the correct PPE, it’s the employer’s duty to supply this. But it is the employee’s responsibility to use the PPE correctly and at the right time.
The Provision and Use of Work Equipment Regulations 1998
PUWER states that any machinery or equipment must be fit for purpose & that anyone using the equipment supplied must be adequately trained to do so.
The Management of Health and Safety at Work Regulations 1999
Employers have a responsibility to carry out risk assessments and review them at the correct intervals, keep records, and create plans to prevent risks. They should also carry out health checks when necessary. There should be a ‘responsible person’ appointed to help an organisation comply with their legal obligations.
Our Training
Our IOSH Approved LOLER Training works to reduce accidents or incidents to employees while lifting operations are taking place. Our course will you help work towards compliance with the regulations.
You will learn what LOLER is, how to select the right equipment, the location of your equipment, the planning lifting operations and maintenance of lifting equipment.
Get started today with a free, no-obligation trial! We also offer a range of Health and Safety training courses.

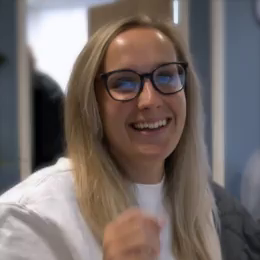
Ellie Johnson
Head of Production
Related articles
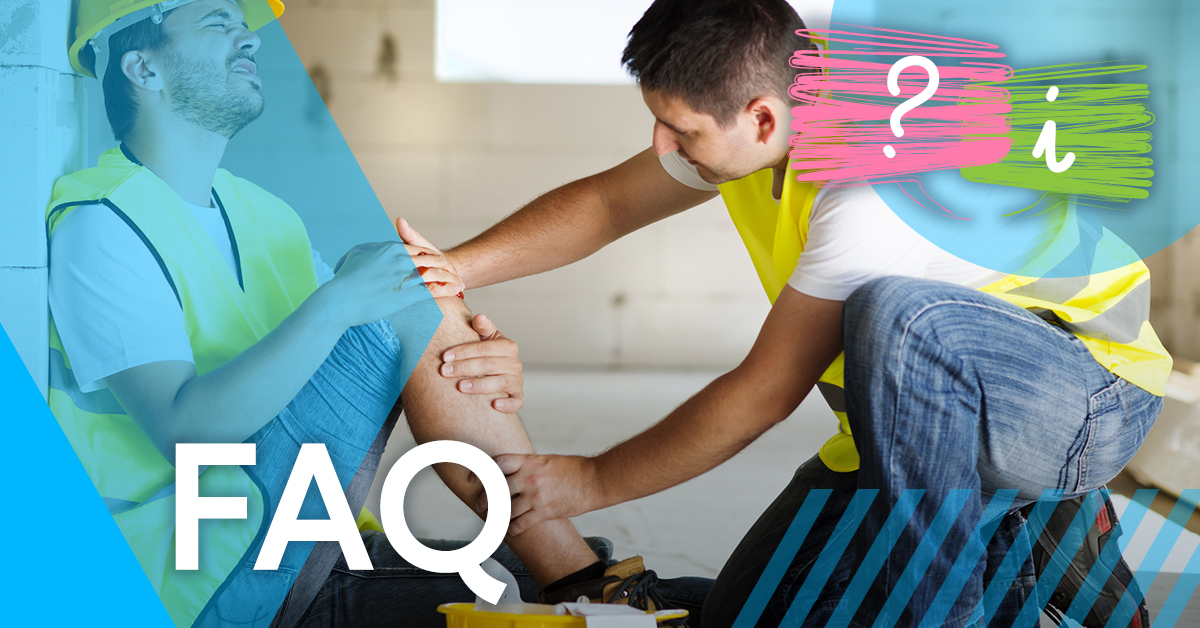
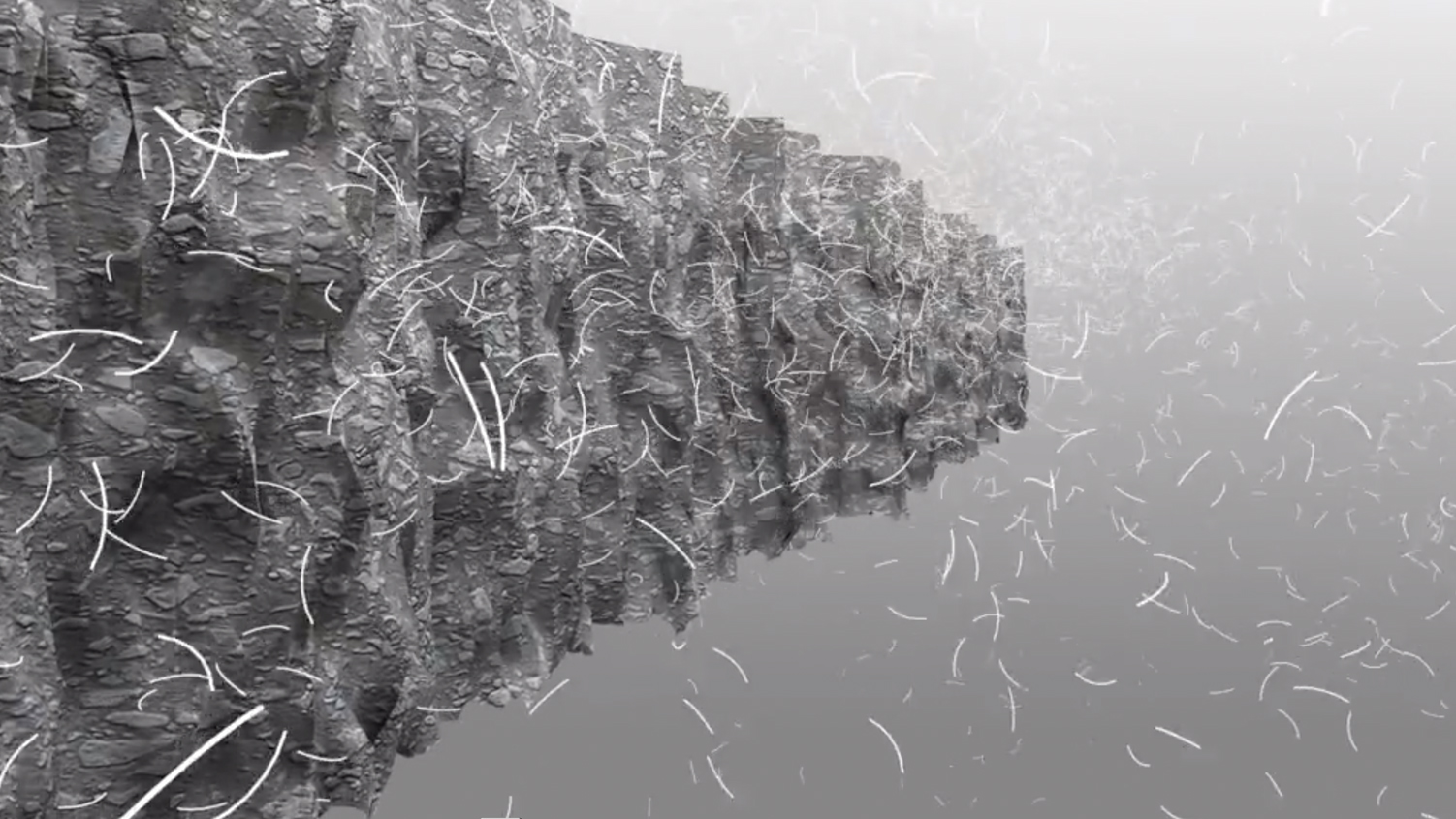
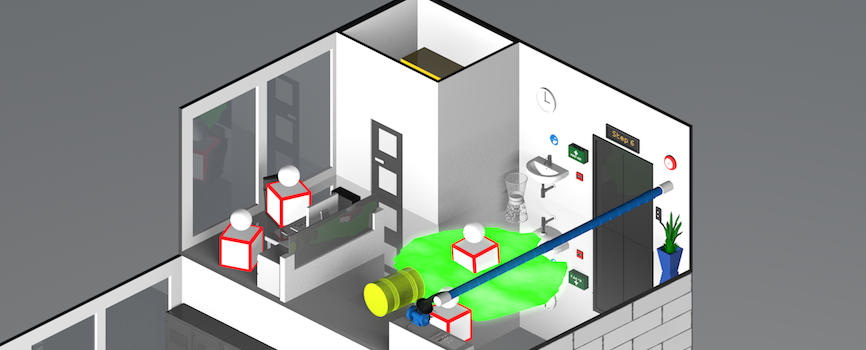
Opt-in to our newsletter
Receive industry news & offers