A guide to Warehouse Health & Safety
Posted 7 years ago
Warehouse health and safety compliance is not something to be taken lightly.
Did you know that warehouse related injuries account for more than 8,500 work-related accidents each year? This is hardly surprising when dealing with vehicles, heavy packages, and dangerous machinery on a daily basis.
Warehouses have plenty of opportunities to be very hazardous working environments. In fact, it’s reported that over 1,600 of these injuries are even considered “major”. For context, a major injury includes fractures and, in extreme cases, amputations, which is why it is so important to ensure warehouse health and safety for everyone at all times.
Poor warehouse health and safety compliance often results in;
- Slips, trips, and falls
- Poor manual handling
- Falls from height
- Being hit by a moving vehicle
- Moving or falling objects
And they are most likely to happen in or around:
- Docks
- Conveyors
- Materials Storage
How warehouse health and safety compliance helps avoid Slips and Trips in a warehouse
Slips
Slips happen when a floor is wet or contaminated. The chances of slipping in a warehouse are higher due to the products that are contained within the warehouse, such as water, oil, cleaning products, foodstuffs… you get the idea! But even things like plastic bags have the potential to cause slips, so make sure you perform checks to ensure all efforts of warehouse health and safety are maximised.
So how do you go about preventing slips in a warehouse?
To honour proper warehouse health and safety compliance, your first priority should be to stop the floor from being contaminated in the first place by maintaining equipment correctly. Should the floor become contaminated, make sure it is dealt with immediately, don’t let it become a hazard for someone else!
You could also look at fitting slip-resistant flooring; this doesn’t mean ripping out your old floor – you can simply buy rolls of slip-resistant flooring that sit on top of the current flooring.
Having the suitable attire especially footwear is also essential. Specifying the proper clothing that minimises injury and adheres to warehouse health and safety compliance is a necessity.
Trips
Good housekeeping is essential, and everyone is responsible for it. Staff should be inspecting the warehouse regularly for any trip hazards and if any are present, they should be cleared immediately.
Warehouse health and safety compliance also includes sensible workflows, and it’s crucial that all storage solutions should be planned.
This ensures any equipment, goods, and waste do not block any walkways.
Check out our Slips, Trips and Falls Prevention Training!
Avoiding poor Manual Handling in a warehouse
With manual handling playing such a significant role in warehouse operations, it should also be a big consideration when stipulating warehouse health and safety practices…It is vital that warehouse staff get this one right!
Conducting poor manual handling over a prolonged period of time can cause nasty musculoskeletal disorders. The most common problems for warehouse staff to encounter are lower back and neck pain.
Manual handling isn’t usually a high-risk task but if it does present a risk, try to avoid carrying out the task in the first place. If it cannot be avoided, do all you can to minimise the risk of injury.
The 4 main things to consider when manual handling are:
- The task
- The load
- The working environment
- Individual capability
To maximise the effects of proper warehouse health and safety compliance, all warehouse staff should be provided with suitable training – and our Manual Handling Training is CPD Accredited, and IOSH approved for your reassurance.
Avoiding Falls from Height in a warehouse
Any work at height (including work carried out for you by a contractor) should always be properly planned and appropriately supervised. If possible, avoid working at height in the first place. Although we understand this isn’t always possible when working in a warehouse environment, and as such, you should make sure you select the right equipment for the work.
Some of the most common falls in warehouses occur when people are working on ladders and step-ladders. Before using a ladder, ask yourself, is this the safest way of carrying out the task at hand? You should be able to show that it’s not practical to use an alternative, safer equipment.
Never use forklifts to access work at height and never climb on racking!
Check out our Working at Height training and Ladder Safety training.
Avoiding injuries from moving vehicles in a warehouse
Inadequate warehouse health and safety compliance has a devastating impact on all involved. Injuries from moving vehicles account for around 25% of all warehouse injuries and generally speaking, the larger the vehicle, the higher chance the injury will be classified as ‘major’.
‘Traffic routes’ should be designed and implemented. Consider:
- The type of vehicle being used
- Minimising the need for reversing
- Avoiding sharp bends if possible
- Maintenance
- Anything that could affect speed/stability (EG slopes)
Try to use a one-way system, but make sure you use vehicles with reversing sensors and or rear-view cameras if this isn’t possible.
When taking in deliveries, visiting drivers should be made aware of any Health & Safety procedures to ensure their safety and the safety of others. It might be worth creating copies of site rules with images to relay the message to people who do not speak English or have a limited vocabulary.
If you have multiple drivers in your warehouse, be sure to check out our Driver Awareness Training!
Avoiding injuries from moving or falling objects in a warehouse
If there are specific areas of the warehouse where objects are more likely to fall, make sure it is clearly indicated and that unauthorised people do not enter the area.
Storage areas must be clearly marked and should avoid tight corners, doors, pillars, and uneven surfaces – all these make falling objects a more likely occurrence!
All pallets should be closely inspected to ensure they are in good condition. If any pallets are damaged, remove them for fixing or destruction. Use stretch wrap to ensure load stability.
Racking should also be inspected regularly and should never be overloaded. There should be three types of inspection:
- Visual inspections at regular intervals
- Expert inspections from a competent person
- Immediate reporting of damage
How iHasco helped Kelly’s Storage
iHasco recently partnered with Kelly’s Storage, a self-storage and records management solution based in Guildford. All of their warehouse staff and drivers lift heavy loads throughout the day…
With many warehouse staff and removal drivers who are continuously lifting boxes, packages and other (much heavier) objects, it was really important for us to find some quality Manual Handling Training that was both time-efficient and easy-to-use. iHasco ticked all of the boxes and the set up was so simple. Thanks to iHasco our staff will have a much better understanding of how to correctly carry out manual handling procedures.
Claim your no-obligation free trial!
Here at iHasco, we offer over 140 Health & Safety, HR, Business Compliance, Management, and Soft Skills Training courses, and many of these courses are tailored to those who regularly work in warehouses. Courses like this will ensure you’re equipped to implement proper warehouse health and safety compliance within your entire business.
Take a look at our Warehouse Training Bundle and claim your no-obligation free trial to any of the courses today!
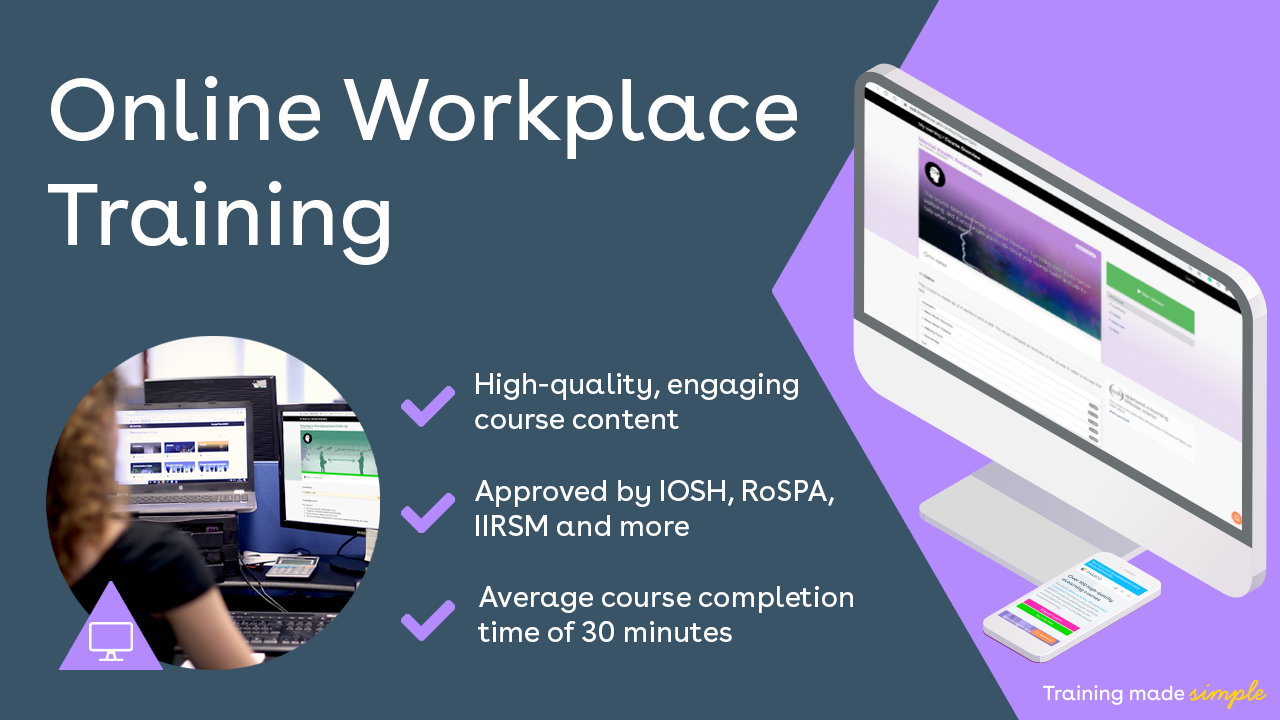
Related articles
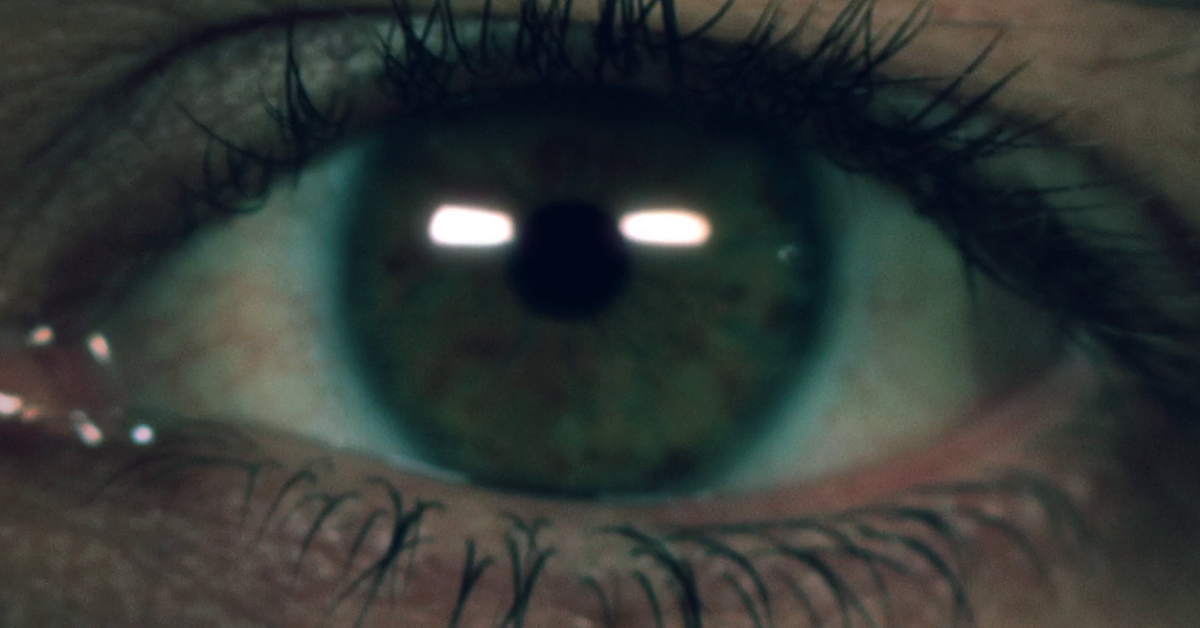
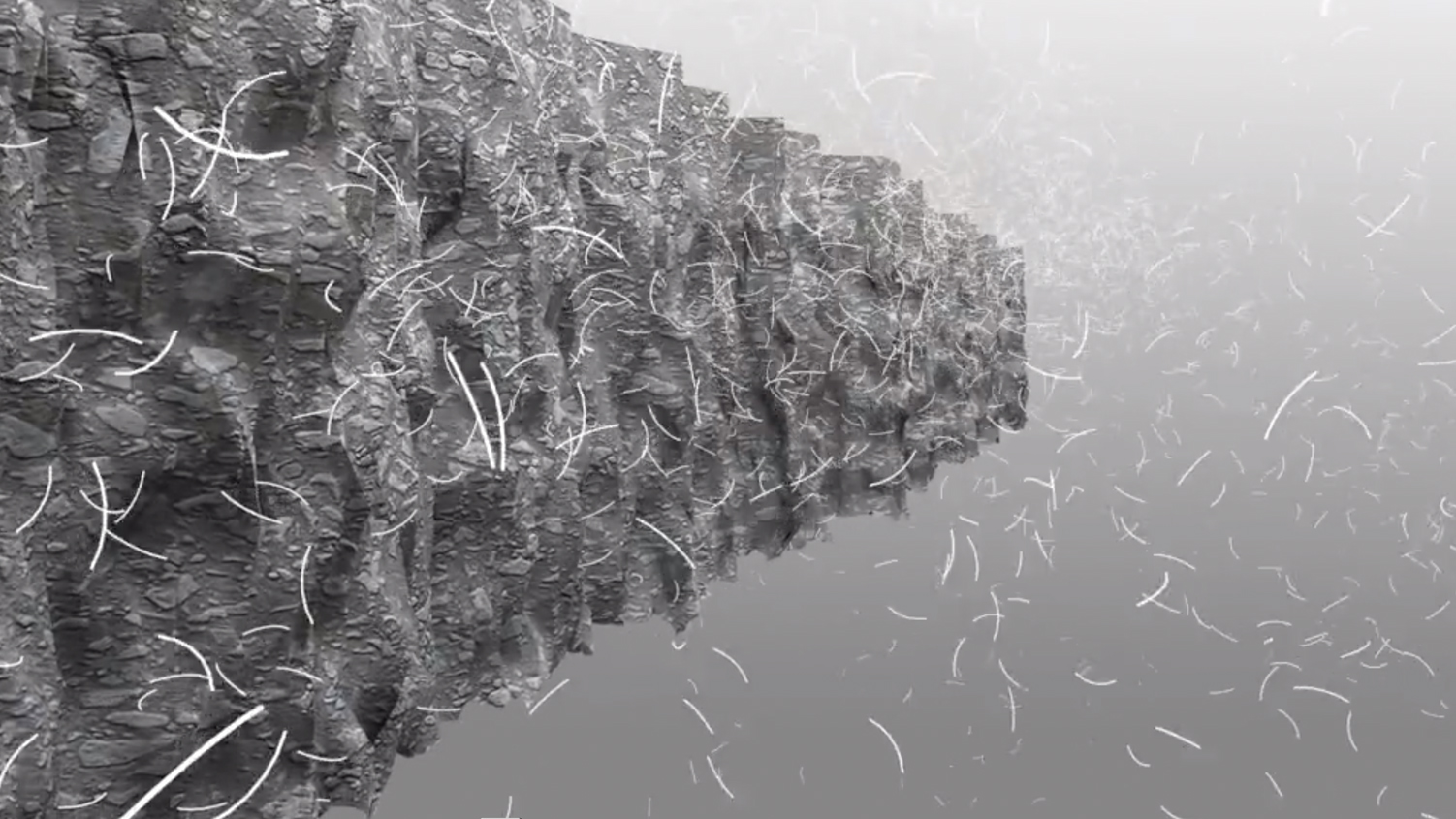
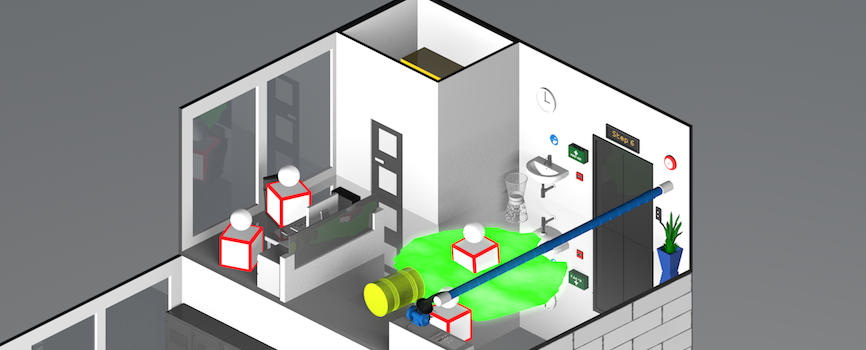
Opt-in to our newsletter
Receive industry news & offers