Can Human Error be avoided in the construction sector?
Posted 9 years ago
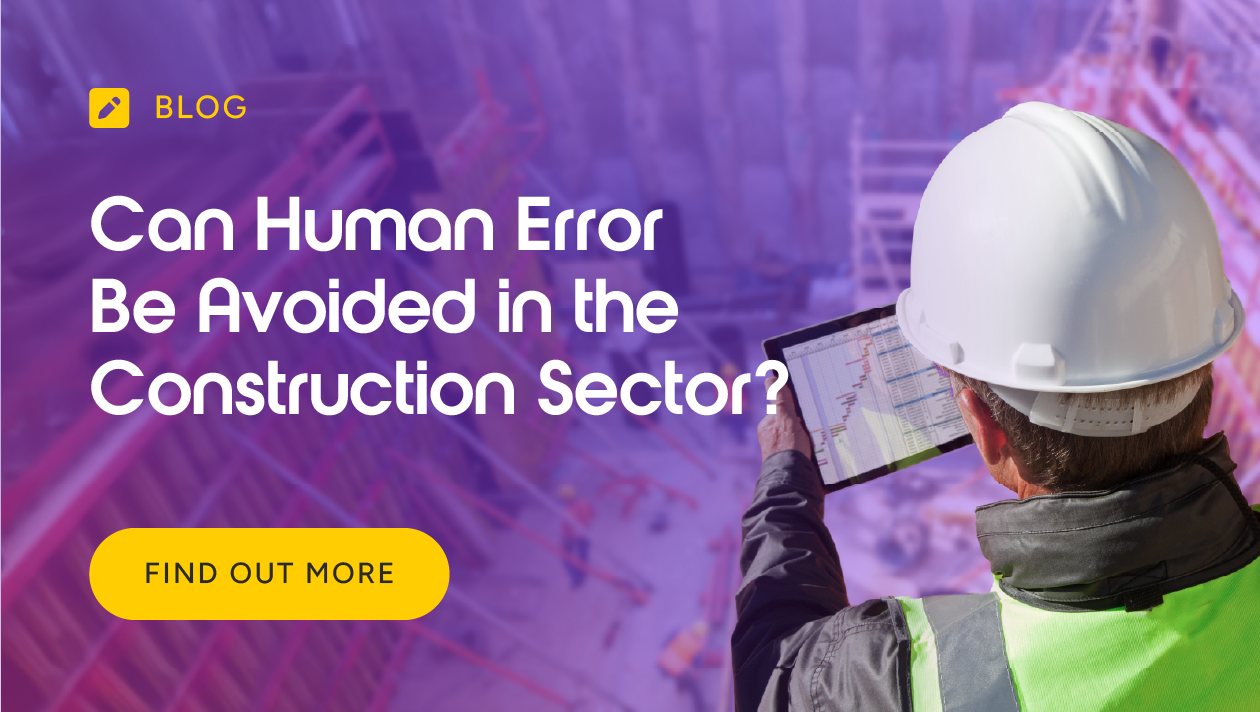
There’s a general assumption that if we removed the ‘human element’, most accidents wouldn’t happen. But is that really the case, or just wishful thinking?
Worldwide, the construction sector is one of the most dangerous industries to work in. In the UK, construction accounts for around 5% of the workforce, yet it’s responsible for 27% of fatal injuries at work and 9% of reported major injuries, according to the Health and Safety Executive (HSE).
It’s a frightening statistic, and one that raises important questions about how accidents happen, and whether human error can ever be completely avoided on-site. While there’s often a perception that incidents are the result of carelessness or poor compliance, the reality is more complex. Let’s take a closer look.
Why human error remains a major issue in construction
Despite strict safety regulations and ongoing improvements across the industry, accidents still occur. And when you look at the most common types of injuries reported by employers, it’s clear many stem from simple but serious mistakes:
- Slips, trips and falls – 31%
- Manual handling injuries – 17%
- Being struck by moving or falling objects – 10%
- Acts of violence – 9%
- Falls from height – 8%
These kinds of incidents often come down to small oversights, poor housekeeping, lifting with the wrong technique, or failing to secure a ladder correctly, to name a few. The reality is that even experienced workers can make mistakes, especially under time pressure or in unfamiliar environments.
And that’s where the problem lies; construction sites are constantly changing. New hazards emerge as work progresses, making it harder to rely purely on routine or experience.
So while it may seem that accidents are commonplace, they’re rarely caused by a single issue. Instead, they often result from a chain of events, decisions, or distractions, many of which involve human judgement.
Is it possible to eliminate human error completely?
In short, probably not!
Human error is a natural part of any workplace, especially in high-risk environments like construction. But that doesn’t mean you can’t reduce its impact.
One model that helps explain why accidents occur is the Swiss Cheese Model. It suggests that in an ideal world, multiple layers of safety defences should prevent incidents. But each layer has ‘holes’ (small weaknesses or lapses), and sometimes, those holes align perfectly, creating a clear path for an accident to happen.
Importantly, this model doesn’t place blame solely on the individual. Instead, it shows how a combination of factors, technical issues, miscommunication, and missing procedures can contribute to an incident.
Still, it’s generally accepted that around 80% of workplace accidents are linked to human error, whether that’s due to lapses in judgement, lack of training, or momentary distractions.
And in construction, where risks can be high, those split-second decisions matter. For example:
- A site worker might skip PPE on a quick job, resulting in a serious injury.
- A manager might miscommunicate safety steps in a toolbox talk, leading to confusion down the line.
- A scaffold might be left unsecured because someone assumed someone else had checked it.
These aren’t acts of malice; they’re often just lapses in attention, routine, or assumptions. And that’s exactly why tackling human error requires more than just more rules; it requires the right environment.
The role of construction safety regulations
The UK construction sector is governed by some of the most robust safety frameworks in the world. Regulations like the Construction (Design and Management) Regulations 2015 (CDM) place legal duties on everyone involved, from clients and designers to contractors and site managers.
Key responsibilities under CDM include:
- Planning work so it can be carried out safely
- Ensuring suitable welfare facilities are provided
- Coordinating efforts between duty holders
- Providing relevant safety information and inductions
But even the best regulations are only effective if people understand and follow them. And that brings us back to the human factor- compliance often hinges on awareness, training, and culture, not just rules on paper.
Can technology help prevent accidents on site?
There’s a strong case for using technology to reduce risk, particularly where hazards are high or conditions are unpredictable.
One recent example comes from Volvo Construction, which is investing in autonomous equipment designed to reduce accidents, emissions, and unplanned downtime. Their goal is what they call “Triple Zero and 10x”:
- Zero emissions
- Zero accidents
- Zero unplanned stops
- 10x greater efficiency
As Volvo’s Uwe Müller explains, autonomous machines can help improve safety in hazardous working environments by removing or reducing the opportunity for human error altogether.
Other examples of tech reducing human risk on-site include:
- Wearable safety sensors, which alert workers to fatigue, noise exposure or hazardous zones
- Drones, used for site inspections and monitoring from a safe distance
- Digital permit-to-work systems, which reduce admin errors and miscommunication
- Augmented reality training helps workers experience and learn to respond to real risks in a safe setting.
While these technologies hold huge potential, they’re not yet a replacement for human judgement, practical training, and strong site leadership. That’s why it’s important to see tech as a support, not a substitute.
How to reduce human error in construction
One helpful framework for understanding human behaviour in the workplace is the Skill – Rule – Knowledge model. This model breaks down how people typically respond to tasks:
Skill-based actions
These are things we do almost automatically, like operating familiar machinery or walking on scaffolding. Over time, repeated tasks become second nature, but this can also lead to complacency if risks aren’t reassessed.
Rule-based actions
Here, we follow clear instructions or procedures, like using PPE or locking off equipment. These actions rely on established rules and on workers’ understanding and applying them consistently.
Knowledge-based actions
When workers face an unfamiliar situation, they rely on judgement and training. In these cases, the quality of training becomes critical to ensuring the right decisions are made under pressure.
By supporting all three of these behaviours, enforcing clear rules, and providing thorough training, you can significantly reduce the risk of human error on-site.
Practical steps to minimise mistakes
Reducing human error doesn’t mean removing the human; it means helping people make better decisions under pressure. Here are some effective steps to take:
- Regular, high-quality training – Refresh workers’ understanding of key risks, not just during induction but throughout the year. Use interactive sessions, real-life scenarios, and short assessments to boost engagement and help knowledge stick.
- Toolbox talks and site briefings – Keep safety front of mind with consistent, focused reminders. Tailor topics to what’s happening that week, like lifting procedures during crane work or PPE reminders in extreme weather, for maximum relevance and impact.
- Clear signage and layouts – Reduce confusion and guide safer behaviour with visual cues placed at key decision points, like entrances, stairwells, hazardous zones, or near machinery. Well-placed signs and site maps help workers navigate safely and reinforce key rules without needing verbal reminders.
- Real-time monitoring – Use technology (like site sensors or digital reporting tools) to track behaviour and site conditions.
- Encourage near-miss reporting – Learning from what almost happened is one of the best ways to prevent what could happen next. A good reporting process should be simple, allowing teams to log incidents quickly so trends can be analysed and future risks addressed early.
- Promote a positive safety culture – Make it easy for workers to speak up, ask questions, or raise concerns without fear. Trained supervisors who listen and lead by example, as well as anonymous reporting channels, can encourage open communication across the site.
It’s also important to look beyond the surface when incidents do occur. Ask not just who made the mistake, but why. Were they under pressure? Was the system unclear? Were they properly trained?
This shift from blame to understanding is key if you want lasting improvement.
While we may never be able to fully eliminate human error in construction, we can certainly reduce its impact. By building safer systems, encouraging open communication, and investing in the right training, construction sites can become significantly safer and more productive.
Technology will play a growing role in reducing risk, but it’s how people use it that really matters. And that’s why giving workers the skills, confidence and knowledge to act safely will always be the foundation of any strong safety strategy.
Effective training at iHasco
It’s one thing to have the right procedures in place, but unless everyone on-site understands and follows them, they may as well not exist.
That’s where training comes in.
At iHasco, we’ve helped thousands of construction businesses strengthen their safety culture through practical, engaging eLearning. From Working at Height and Manual Handling, to Asbestos Awareness and Fire Safety, our courses are designed to support frontline workers with the knowledge they need, wherever they are.
Our training is also built with real-life scenarios in mind, helping workers understand not just the rules but the why behind them, reducing the chance of mistakes when it matters most.
Because human error isn’t just about forgetfulness or carelessness, it’s often a sign of missing information or unclear expectations. And when those gaps are filled, everyone benefits.
Why not try our free, no obligation trial today to find the best course for your business, or simply request a quote today to find out more!
Related articles
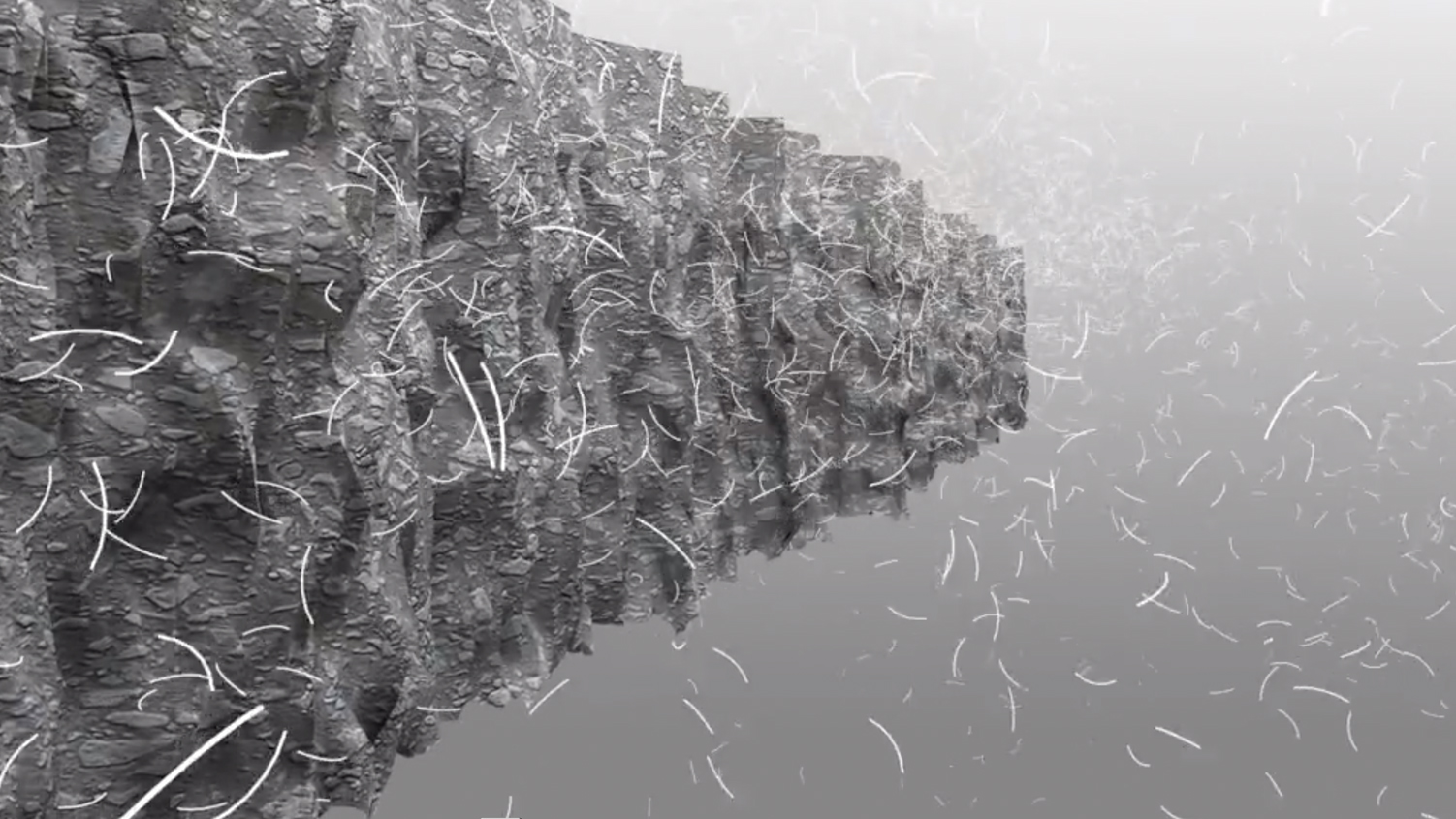
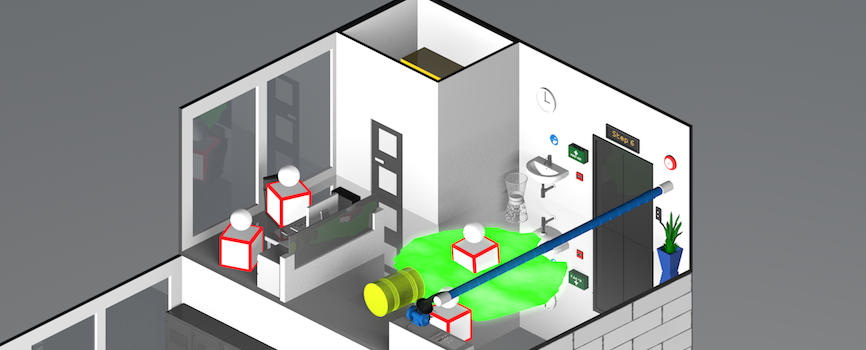
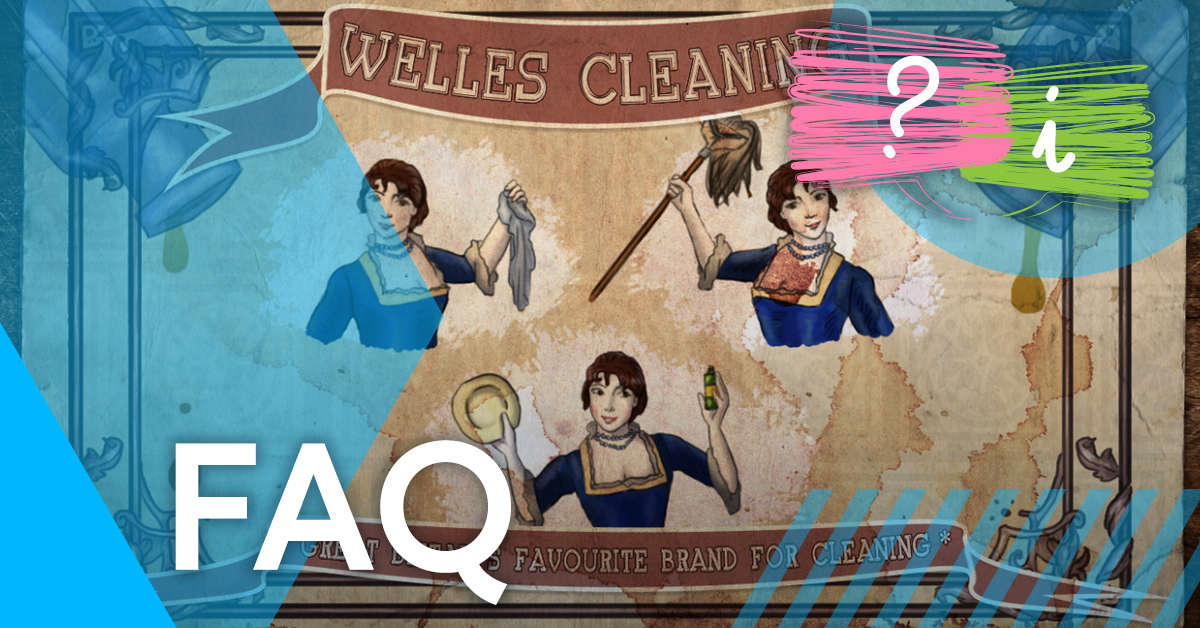
Opt-in to our newsletter
Receive industry news & offers