What are the Manual Handling Operations Regulations 1992?
Posted 4 years ago
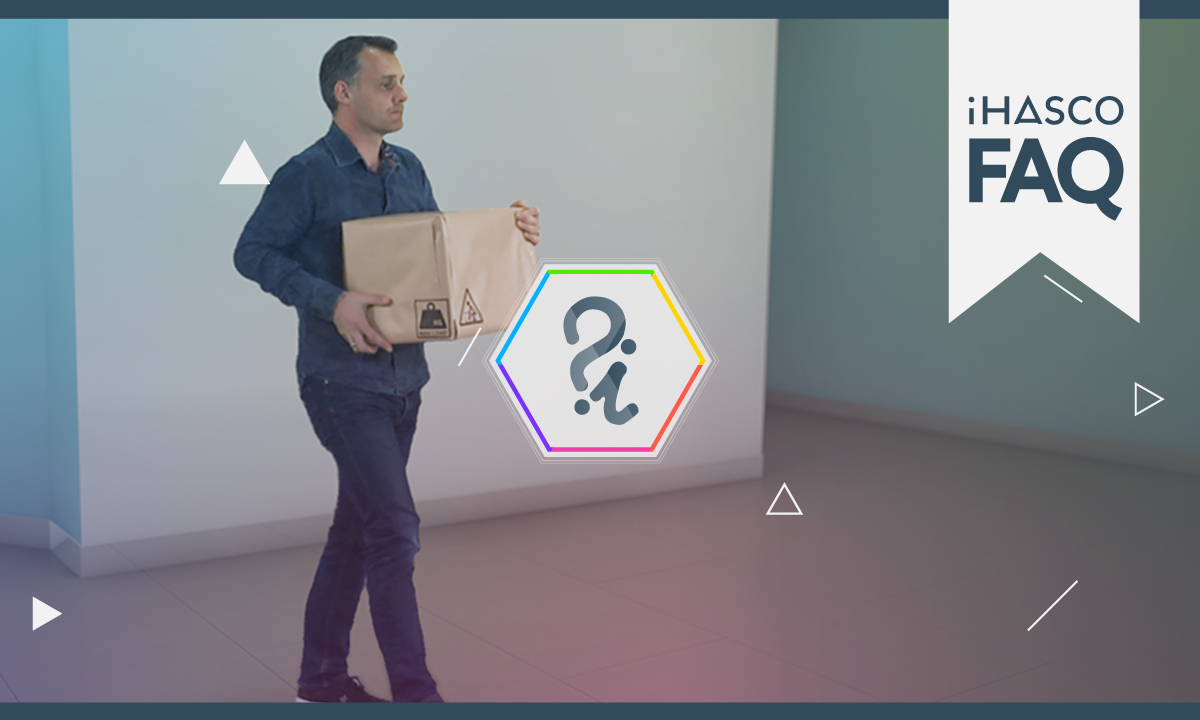
With manual handling injuries accounting for one in three workplace injuries in the UK, and also being the main cause of roughly 300,000 individual cases of back pain, it is crucial that employers and their staff understand their responsibilities under the regulations.
Manual handling practices take place in many different workplaces by a variety of employees, so it is important that these people are educated to understand what is considered manual handling and how to safely practice it.
The Manual Handling Operations Regulations 1992 (MHOR) define manual handling as:
any transporting or supporting of a load (including the lifting, putting down, pushing, pulling, carrying or moving thereof) by hand or bodily force.
A load is defined as an object, animal or person.
The regulations require individuals to consider the following points, in order, when assessing the risks associated with manual handling:
- See if you are able to avoid the lift altogether and eliminate the risk
- You need to assess the risk of the operation if it can’t be avoided
- Once you have assessed the risk find ways to reduce it
A more memorable way of putting it is AVOID, ASSESS, REDUCE!
Employers have a legal duty to ensure, so far as is reasonably practicable, the health, safety, and welfare of all their employees. With that said, under the MHOR, employers must make a sufficient assessment of the risk to employees when performing manual handling operations when they pose a risk of injury.
Additionally, employees also have a duty to take care of their own health, safety, and welfare, as well as others who may be affected. This requires all employees to communicate effectively with their employers and raise any concerns they might have about their manual handling tasks so that they can be reviewed.
Good manual handling practices
When carrying out a manual handling task, there are three main things to consider: the weight of an item, the amount of time you have to carry an item, and if there is any twisting, stretching, or other bad posture you may adopt in a task.
With that said, there are a number of good manual handling practices that a person and organisation can implement in order to lower the risk associated with the task.
Firstly, a person should always lift with their Power Zone.
The Power Zone is the space between your mid-thigh and mid-chest where you can lift the most with the least amount of exertion.
See an example of the Power Zone below:
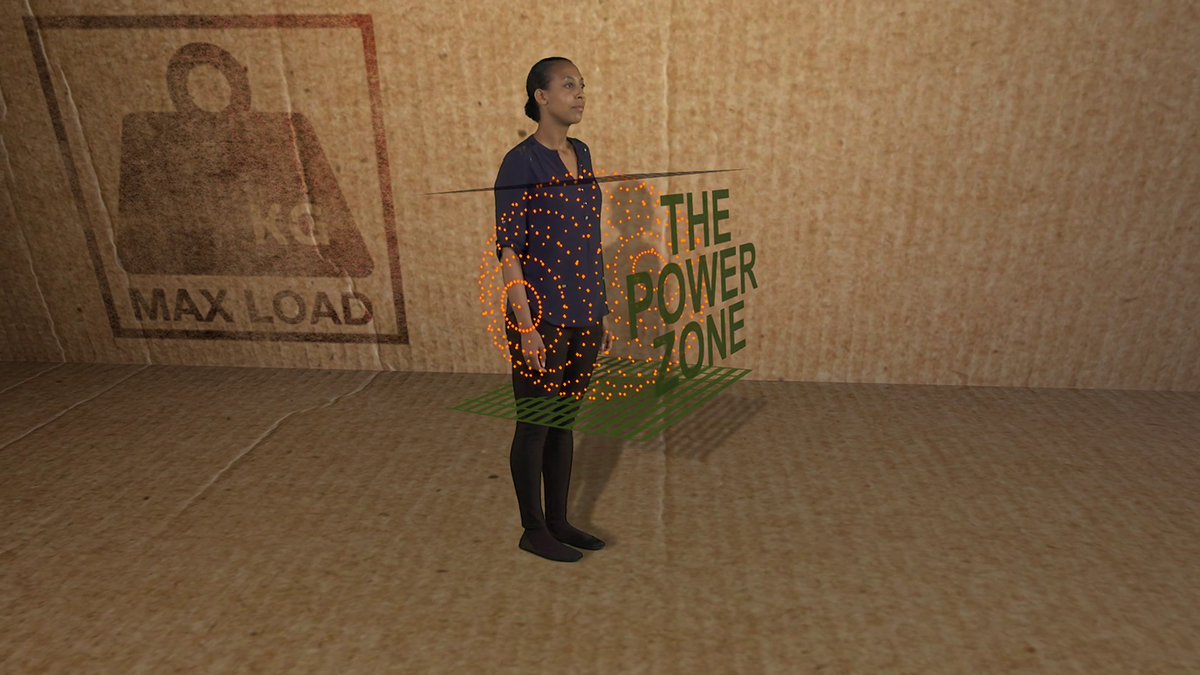
Additionally, another important thing to remember when carrying out a manual handling operation is to complete a LITE (also known as TILE) assessment.
LITE is an acronym that stands for:
- Load
- Individual
- Task
- Environment
These are the four things that should be assessed before attempting any manual handling task.
For more information about LITE assessments, see our blog!
Finally, when lifting, you should always try and keep a neutral posture. This means your spine is aligned, not twisted, and your joints shouldn’t be bent. This also means that your body is balanced, and any weight you’re carrying is evenly distributed.
It isn’t possible to maintain a neutral posture all of the time, but you should try as often as you can, especially when you’re manual handling.
The aim is to minimise the stress that’s placed on your muscles, tendons, nerves and bones.
Other relevant legislation
There are a number of other regulations, acts, and pieces of legislation that relate to manual handling practices, and it’s important that employers are aware of their legal obligations.
The Health and Safety at Work Act 1974
The Health and Safety at Work Act 1974 ensures that employers are responsible for taking care of their employees and that they have the best interests of their employees in mind.
It shall be the duty of every employer to ensure, so far as is reasonably practicable, the health, safety and welfare at work of all his employees.
The Lifting Operations and Lifting Equipment Regulations 1998
The Lifting Operations and Lifting Equipment Regulations 1998 aims to make lifting operations and the use of lifting equipment as safe as possible.
Lifting operations should be planned, supervised and conducted safely by competent people.
The Management of Health and Safety at Work Regulations 1999
Under the Management of Health and Safety at Work Regulations 1999, employers must:
- Carry out risk assessments where necessary and regularly reviewing them
- Keep records of injury and incidents
- Plan preventive measures
- Carry out health checks to ensure employees are able to perform certain duties
Additionally, under these regulations, employers are required to ensure that their employees are provided with adequate health and safety training.
Online Manual Handling Training
Here at iHasco, we offer an Online Manual Handling Training course that can be completed in just 35 minutes.
The IOSH Approved eLearning educates employees on how proper manual handling is quite simple. The course, which is broken down into 4 easily-digestible sections, also covers LITE systems, what needs to be considered before lifting, and proper manual handling techniques.
Claim your free, no-obligation trial to the course today!
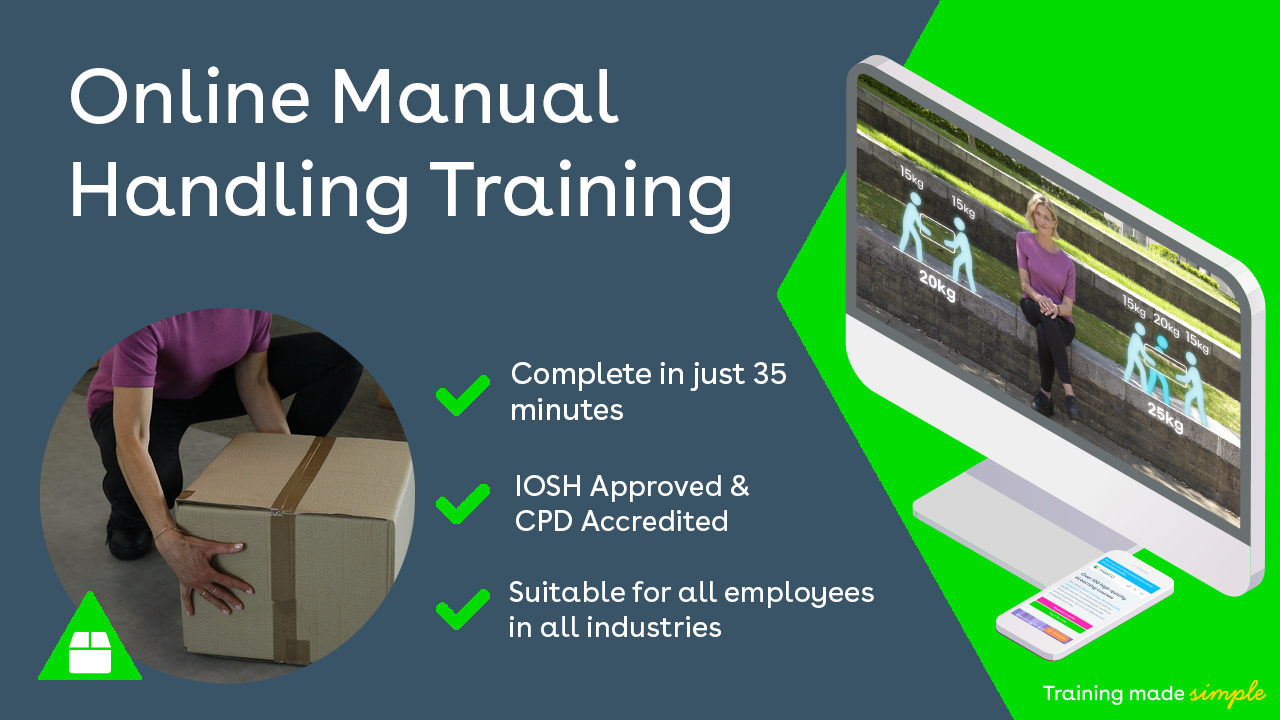
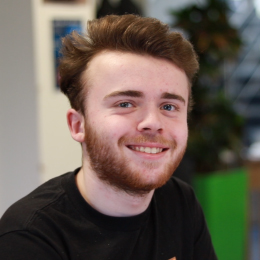
Jack Rosier
Senior Marketing Executive
Related articles
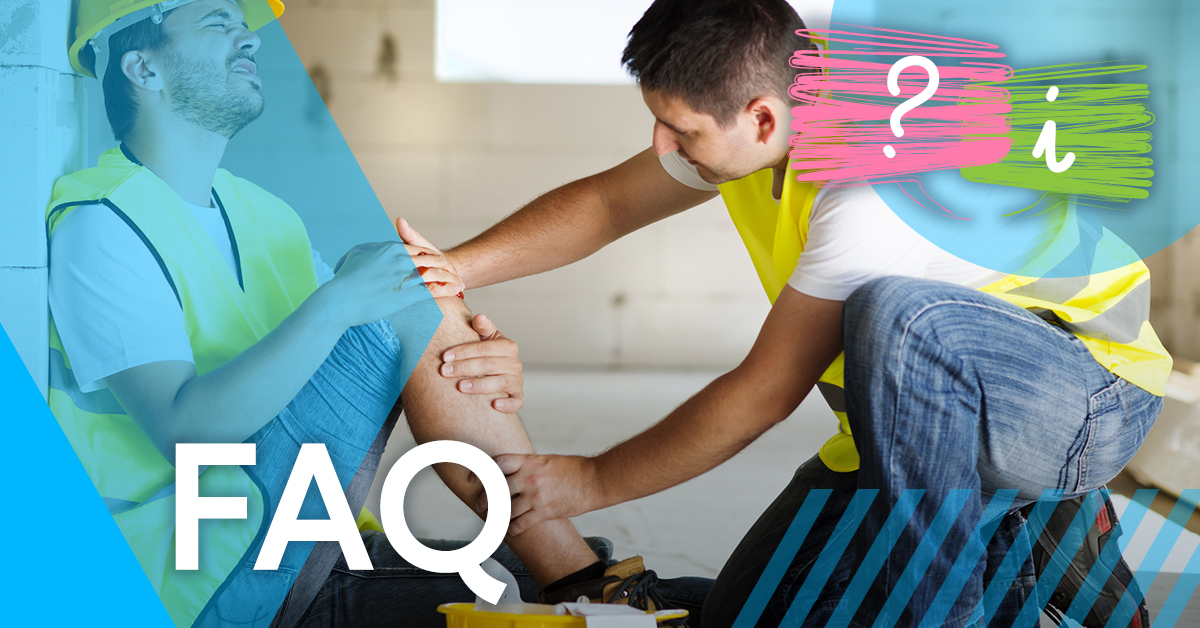
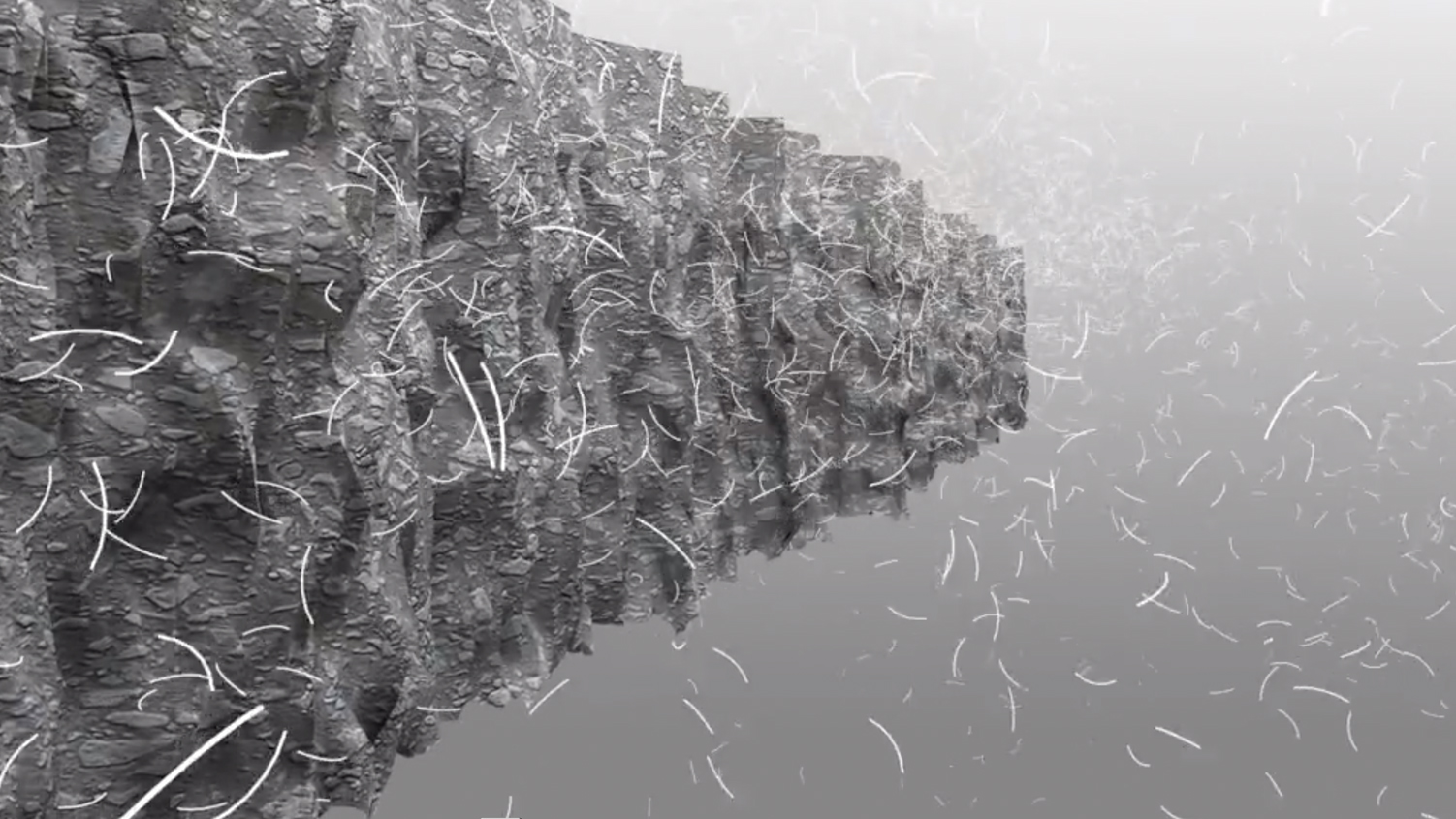
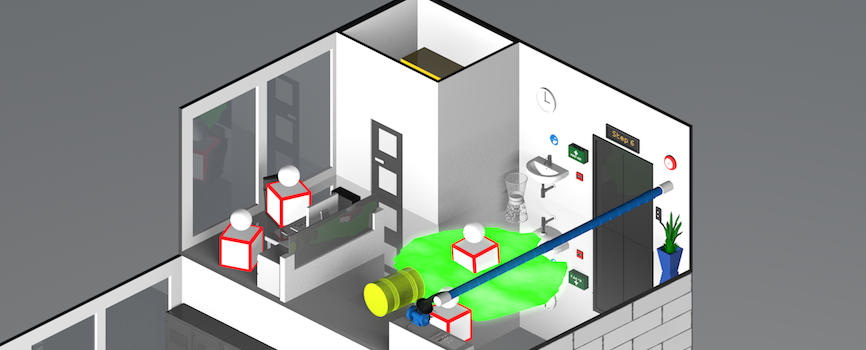
Opt-in to our newsletter
Receive industry news & offers